Win-Win: Advanced Antifouling Saves Both Money and the Environment
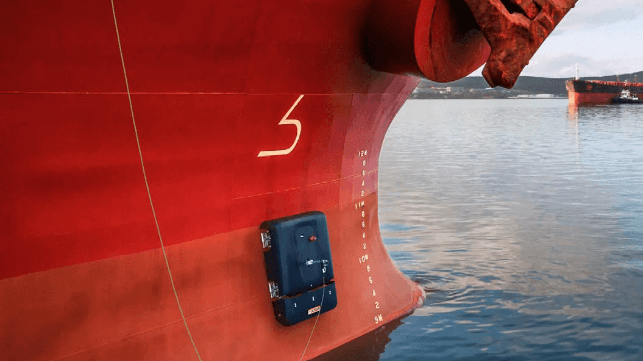
(Article originally published in Mar/Apr 2024 edition.)
Shipowners have been looking for ways to keep the weeds and barnacles off their vessels since time immemorial. Enterprising Greek traders began using lead sheathing as early as the third century BCE, and the Royal Navy pioneered the use of sheet copper in the mid-1700s.
In those days, it was common to take extreme measures to access and clean the hull – like winching the whole ship 45 degrees over at the dock, ballasting to create a severe list at anchor or intentionally grounding on a tidal flat.
Luckily, owners today don’t have to endanger their vessels to get the job done, but the incentive to keep the hull clean remains the same. Heavy fouling can increase fuel consumption by up to 40 percent, according to the IMO GloFouling project. With VLSFO trading at up to $700 per ton, the extra drag can easily cut into earnings.
Carbon taxes
The cost impact will become more pronounced as regulators begin to tax carbon.
It’s already happening for vessels that call in the E.U., where owners have to buy Emissions Trading System (ETS) allowances for 40 percent of their emissions. In recent years, ETS allowances have traded between $60-100 per ton of CO2. With three tons of CO2 produced by every ton of bunker fuel, this cost adds up fast.
A similar carbon price structure may be coming soon for shipowners around the world.
The IMO is gradually moving toward a bunker levy to raise funds for green fuel, and Secretary-General Arsenio Dominguez says he’s “very confident” there will be some form of carbon pricing mechanism by next year. Some proposals seen at IMO would set the tax as high as $150 per ton of CO2, though industry-backed rates would be far lower.
While the details and timing will be debated, the takeaway for the owner is that the cost of bunkering could get much higher, and soon. That makes fuel-saving interventions more valuable than ever, and advanced antifouling is one of the simplest and most cost-effective changes an owner can make to cut carbon.
Without altering the engine, installing new equipment or finding a new green energy source, it’s possible to reduce emissions by double-digit percentages simply by spraying on a better antifouling at the next drydocking. There are lots of factors that go into the exact number, including the owner’s commitment to proactive maintenance between dockings, but careful research by AkzoNobel (among many others) proves that – apples to apples – it’s possible to predict meaningful savings from applying an advanced coating to an existing ship.
Double-digit savings
One of the first big alternatives to traditional antifouling is still one of the most effective options out there. Since its launch in 2013, Hempel’s Hempaguard has been used on 4,000 ships of all types, and the number is growing.
By Hempel’s calculations, its top-end hull coatings reduced the maritime industry’s CO2 emissions by 6.5 million tons last year alone. (That’s like taking 1.4 million cars off the road.) If a shipowner wishes to see how it would do on their particular ship, Hempel can forecast the vessel’s performance with and without Hempaguard, based on prior vessel data and advanced computer modeling.
Hempaguard is a silicone-based foul release coating. Compared to the average anti-fouling coating, Hempaguard delivers up to a 20 percent CII (carbon intensity indicator) improvement over the course of a drydocking cycle, says Davide Ippolito, Director, Solution Management at Hempel. The low-friction coating gives an immediate efficiency boost out of drydock and keeps speed loss to just one percent between five-year docking periods.
Its formula contains small amounts of biocide – about five percent of the amount found in self-polishing coatings – and this makes it resistant enough to heavy fouling pressure that Hempel recommends it for all vessels on all routes.
“It’s a no brainer when it comes to finding market-proven solutions to reduce fuel consumption and lower emissions at fast ROI,” Ippolito says. “With the E.U.’s ETS regulations shaping purchasing decisions for owners and operators of vessels trading in European waters, there’s an even greater incentive today and moving forward.”
Hempel is not resting on its laurels, though. It continues to invest in R&D, and Ippolito says more innovation will be needed for a long time to come. Beyond the chemistry, there’s also work to be done on improving lifecycle performance through proper management.
“While coatings play a crucial role, holistic fouling management practices, including performance monitoring, hull cleaning and biosecurity measures, are essential to maintaining optimal vessel performance and compliance,” he explains. “Additionally, regulatory pressures and evolving environmental concerns necessitate continuous improvements in fouling prevention and control strategies.”
Proven performance
Jotun pioneered silyl acrylate antifouling more than two decades ago and remains a leader in this segment today. When combined with its Hull Performance Solutions system, the technology provides a measurable fuel savings of 15 percent compared with the average antifoulant on the market, the company says.
It starts with a choice of two premium grades of silyl acrylate coating infused with biocide to resist challenging fouling conditions. Jotun says its coatings, too, have been proven to work with a loss of speed of just one percent over five years. (By way of comparison, the market average speed loss is about six percent.)
But it’s more than the formulation of the product. The solution is part of a package of data-driven analysis, technical services, and performance guarantees for the owner.
For shipping companies that really want to go the extra mile, Jotun sells a system designed for proactive, regular cleaning. It created a specialized version of its foul-release coating to work with a robotic device called HullSkater, which scrubs the hull without the need for divers in the water. Jotun’s own staff can operate the HullSkater remotely, 24/7, wherever the ship is located – even when at anchor.
“We could see that Jotun’s [Hull Skating] concept addressed all the challenges in one idea,” says Geir Fagerheim, SVP Marine Operations at Wallenius Wilhelmsen, who worked with Jotun during development. “They are looking at this as a solution – a clean hull as a service rather than paint as a product.”
Percolating over
Advances in marine technology often start in other industries and percolate over, and one of the most promising new foul release products started life in an R&D project for a big-name aerospace company.
GIT Coatings’ CEO Mo AlGermozi and CTO Marciel Gaier met in a university lab while designing a low-friction, graphene-based coating for aircraft landing gear. As they looked at different applications for the new formula, they tried it out in high-flow water pipes in hydroelectric dams and found they could achieve improvements in efficiency.
That’s when it occurred to them to test it in a maritime application, and they applied the coating to the hull of a local businessman’s yacht. “One day the owner gave me a call and said, ‘Mo, you know, we saved about 150 bucks this week on just a couple of trips,’” AlGermozi recounts.
Seven years later, GIT’s products are on all kinds of vessels, from cruise ships to product tankers, and it’s fast becoming a familiar name in the maritime industry. The company makes two eco-friendly, graphene-based formulations: a propeller coating, XGIT-PROP, and a hull coating, XGIT-FUEL. The propeller coating alone can improve vessel performance by as much as four percent – without biocides, silicone oils or microplastic shedding.
Shipowners often start with the prop coating to try the product line out since the initial outlay is low and the payback time is just a few months. Recent adopters include bulker specialist Pacific Basin, which is rolling out XGIT-PROP on 40 vessels this year. “At a fleet-wide level, we anticipate significant reductions in both environmental impact and operational expenses,” says Sanjay Relan, General Manager of Optimization at Pacific Basin.
In addition to the efficiency gains right out of drydock, GIT says its products are easy to apply and hold their edge over time. The graphene coating is hard and durable and, depending on the vessel and its operating profile, a coat of XGIT-FUEL might be usable for up to 10 years before a full blast and recoat (though many owners choose a standard five-year cycle).
The environmental benefits of a graphene coating are high on AlGermozi’s list of priorities, and it’s not just the CO2 reduction. It’s also the reduction of pollutants in the water column. “There are 16 different biocides and active materials that can be used globally,” he explains. “In 2024, that list will go down to 10 biocides. Our hope is that, over the next 10 years, these toxic coatings are phased out. We’re ready for that with a hard coating that can be cleaned when necessary.”
Keeping history afloat
Before applying antifouling coatings, a ship must first have a well-prepared hull surface. As vessels age, this often means repairing corroded sections of plating.
The traditional way to go about it is to cut out and replace thinned areas wholesale, but modern epoxy repair compounds give the shipyard a new, class-approved way to get the job done fast. Belzona says these compounds yield long-lasting repairs below the waterline, even on hard-wearing surfaces like a thruster on an icebreaker or a discharge pipe from a scrubber.
Belzona’s repair compounds have also found a following among operators of historic vessels and museum ships, which may be challenging to weld on because of their age and condition. For these ships, a careful application of a filler epoxy restores hull integrity without imposing the stresses of hot work on the structure.
Prominent customers include the USCGC Taney, the last warship to survive Pearl Harbor; the WW II submarine USS Bowfin, and the WW I cruiser HMS Caroline. These repairs literally keep history afloat for the next generation of mariners.
The opinions expressed herein are the author's and not necessarily those of The Maritime Executive.